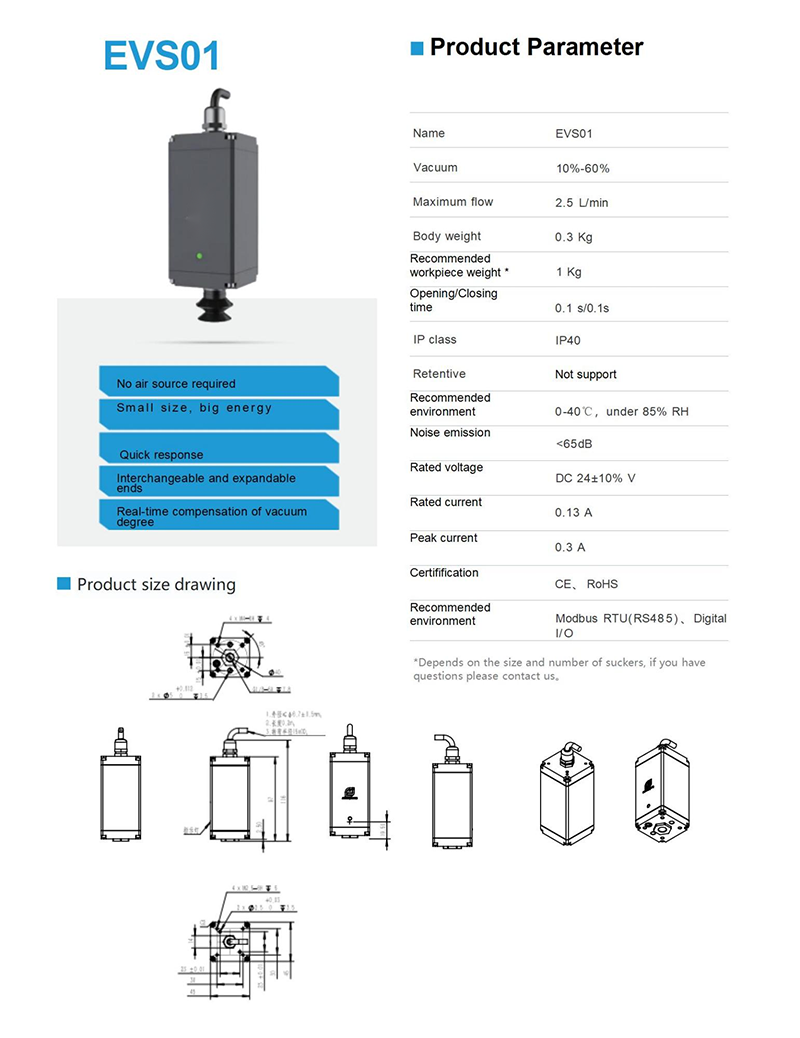
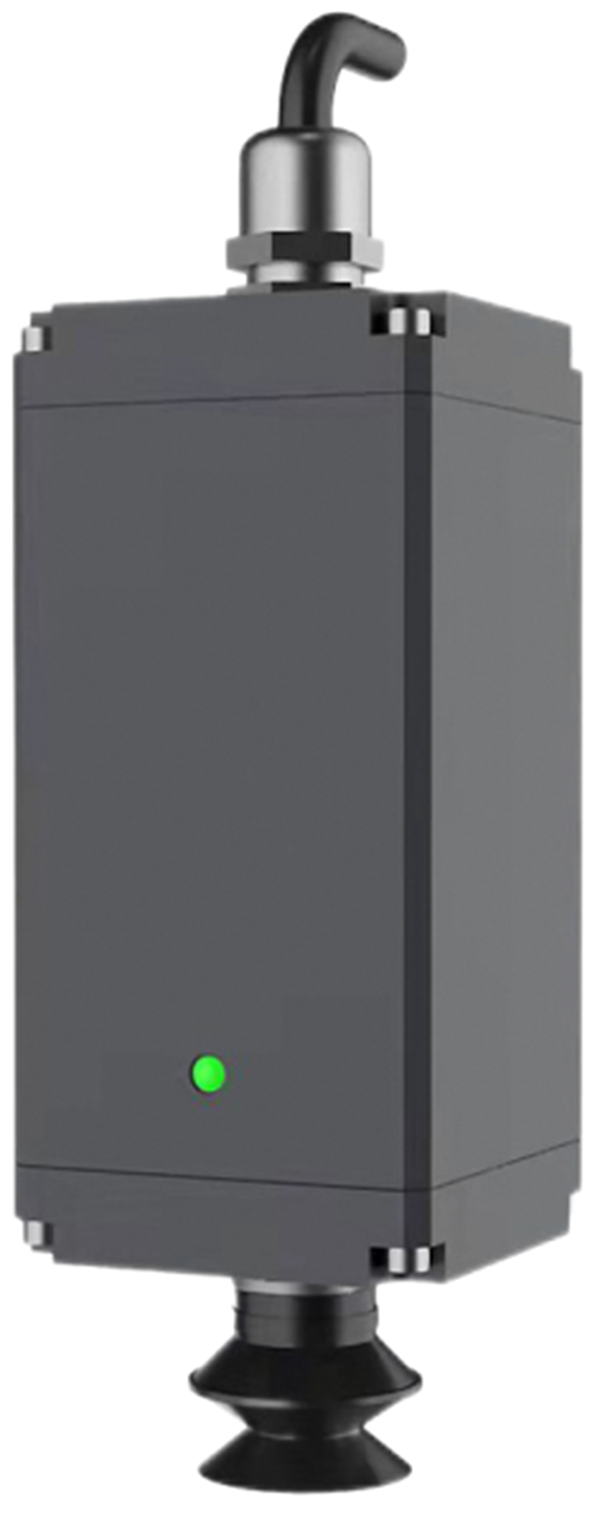
From the perspective of functional structure, the execution of the vacuum generator is mainly the electromagnetic control valve to control the vacuum generator to realize negative pressure generation and stop, so as to achieve the function of attracting and releasing the workpiece.
As a result, the system generally includes the following components: 1. Compressed air source; 2. Filter; 3. Switch solenoid valve; 4. Vacuum actuator; 5. End suction cup, air bag, etc. (A typical structure is shown in the figure below).
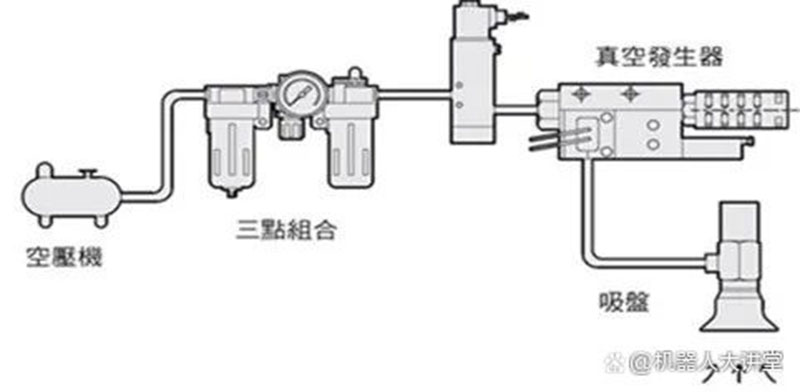
In addition, under the requirements of industrial automation, in order to realize the monitoring of the vacuum adsorption process, some manufacturers generally add pneumatic control components such as flow meters, pressure detection switches, and proximity switches to the system in recent years.
However, since most of the components are modified by the integrator according to customer needs and on-site working conditions, the complexity of the entire system is often high.
At the same time, multiple component manufacturers lead to complex installation and commissioning work on site, and some of them have high energy consumption and 100% dependence on gas sources. Partial integration may not be possible
Avoid noise pollution, which means unacceptable problems for high-precision and high-clean environments such as lithium batteries and semiconductors.
On the whole, EVS is a new generation of electric intelligent vacuum actuator that does not require an additional compressed air source, which is undoubtedly eye-catching.
The biggest benefit of the air-saving system is its ease of installation. Because this can undoubtedly reduce many auxiliary components, including air compressors, air storage tanks, air purification equipment, and output pipes, etc., making wiring easier and more convenient and clear for customers to use.
It is reported that at present, many scenes including mobile robot platforms, 3C electronic assembly, lithium battery manufacturing, semiconductor manufacturing, express logistics, etc. have a relatively compact space layout.
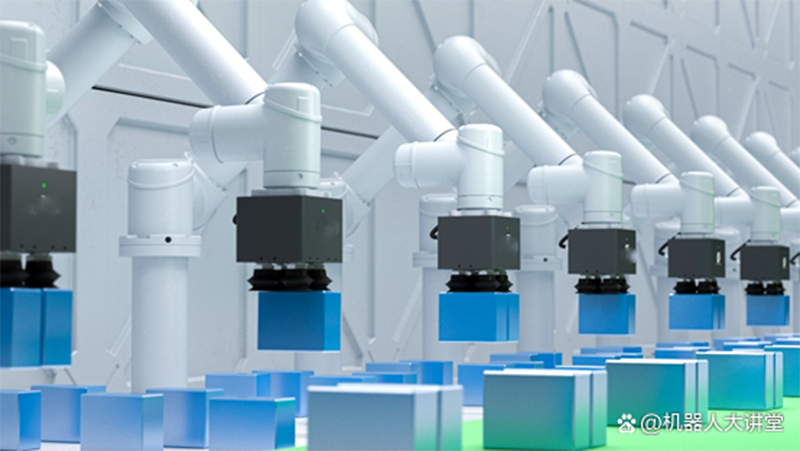
EVS08 suction square battery
More details and advantages
The robot lecture hall learned that this product, which looks very small and weighs only 2.5kg, can reach a high level of 10kg. Due to the 24V low-voltage design, the energy consumption is 20% of the traditional pneumatic system, and the adsorption force at the end can be set and adjusted, and the adsorption force can reach 102-510N.
In terms of structural design, EVS adopts a more compact and lightweight structural design, which makes EVS 30% smaller than traditional aerodynamics for the same weight of load.
At the same time, it can be directly connected to the connector at the end of the robotic arm, which reduces redundant auxiliary components, makes it more flexible to use, can be quickly deployed, and can easily absorb multiple large objects, especially suitable for stacking, handling and other scene operations .
In order to improve the convenience of use, the electric vacuum actuator also has an integrated interface, which can be used to control and monitor the whole process of adsorbing objects.
It is reported that this is for the convenience of customers to control the vacuum degree of the vacuum actuator through instructions, and also connect through the IO link for monitoring and predictive maintenance of the adsorption process. Status monitoring will reduce errors and downtime and ensure system availability.
On this basis, the advantages and characteristics of EVS are also reflected in the following points:
1. Compact structure and light weight: EVS is 30% smaller than the traditional pneumatic size when absorbing the same weight of load. It can be connected with the connector at the end of the mechanical arm to realize the absorption of the load, especially suitable for stacking, handling and other scene operations;
2. Abundant terminal configuration: Various types of suction cups, airbags and other components can be configured to realize the grasping of different objects, including square, spherical and special-shaped components;
3. Dual channels can be controlled independently: easily control the left and right sides of the vacuum actuator, and the two sides are independent of each other, further improving the working efficiency of the production line. It realizes suction and placement at the same time, which greatly facilitates the handling and sorting of objects, saving space and time;
4. Adjustable suction: the degree of vacuum can be adjusted according to the characteristics of the sucked product, and real-time vacuum compensation can be realized;
5. Status feedback: It has a vacuum feedback sensor, which can detect the adsorption status of objects in real time, and provide feedback and alarm;
6. Power-off protection: After power-off, it can realize adsorption power-off self-locking to protect the adsorbed objects;
7. Strong adaptability: support 24V I/O and MODBUS RTU (RS485) communication protocol;
8. Easy to install and debug: the communication protocol is simple and readable, which greatly reduces the difficulty of debugging. In addition, the host computer debugging software can be attached as a gift, which can be set and edited to set function parameters offline.
Conclusion and the future
Under the trend of automation and intelligence, electric vacuum actuators have increasingly become a key component to ensure the normal operation of robots and automation systems, making the use of electric actuator systems more convenient and easy to use, and can meet more diversified scenarios such as mobile composite robots. .
The integrated interface and rich terminal configuration and other optimizations can further improve the reliability of the key components of the robot, reduce production stoppages and remote deployment problems for end users, and further reduce maintenance and after-sales costs.
Post time: Apr-19-2023